玻璃钢吸收塔生产中的材料浪费:现象、原因及应对策略
在工业生产领域,玻璃钢吸收塔因其卓越的耐腐蚀性、轻质高强以及良好的综合性能,广泛应用于化工、环保等行业的废气处理与净化环节。然而,在其生产过程中,材料浪费问题却如同隐藏在暗处的“利润杀手”,不仅增加了生产成本,还对资源环境造成了一定压力。深入剖析这一现象,探寻有效解决之道,成为玻璃钢行业可持续发展的关键课题。
一、玻璃钢吸收塔生产中材料浪费的常见表现
(一)原材料过量使用
1. 树脂用量把控失准
树脂作为玻璃钢的关键基体材料,在调配与铺设过程中,若因缺乏精准计量设备或操作人员经验不足,常出现树脂用量超出设计标准的情况。过量的树脂不仅使材料成本攀升,在固化过程中还可能产生气泡、开裂等缺陷,影响吸收塔的整体质量与性能。例如,在一些手工糊制环节,工人为追求施工便利,随意增加树脂涂抹量,导致局部树脂堆积,固化后形成富树脂层,降低了结构层的玻纤含量,削弱了塔体的强度与刚性。
2. 玻璃纤维增强材料过度铺设
玻璃纤维是赋予玻璃钢高强度的主要骨架材料,但在生产中,部分企业为保证产品所谓的“绝对强度”,往往过度铺设玻璃纤维布或毡材。一方面,过多的玻纤增加了材料的消耗与成本;另一方面,不合理的铺设层次与方式会导致纤维分布不均,出现应力集中点,降低产品的稳定性与耐久性。如在缠绕成型工艺里,若缠绕角度、张力控制不当且玻纤层数过多,会使吸收塔在受压时局部受力过大,加速老化破损。
(二)边角废料处理不当
1. 切割余料废弃
在玻璃钢吸收塔的板材切割、零部件加工过程中,会产生大量形状不规则的边角余料。由于这些余料尺寸较小、形状各异,难以直接用于后续生产,许多企业将其当作废弃物处理,这不仅造成原材料的直接浪费,还增加了废料处理成本与环境负担。例如,在制作塔体外壳板时,圆形或弧形板材的边缘切割会留下楔形余料,若不及时回收利用,日积月累数量可观。
2. 不合格品丢弃
生产过程中难免会产生一些不符合质量标准的次品或废品,如内部存在气泡、表面不平整、尺寸偏差过大的吸收塔部件。一些企业缺乏完善的质量管控与修复机制,对这些不合格品简单粗暴地予以报废处理,而实际上部分产品经过适当修补、调整后仍可满足使用要求,这种处理方式无疑加剧了材料浪费程度。
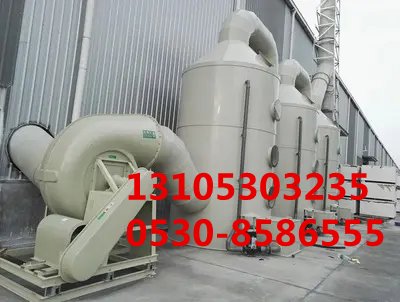
(三)库存积压与过期损耗
1. 市场预测失误导致库存积压
玻璃钢吸收塔的生产周期相对较长,若企业在市场需求预测上出现偏差,盲目扩大生产规模,易造成成品库存积压。长时间存放的库存产品不仅占用大量仓储空间,还需投入人力物力进行维护管理,而且随着时间推移,库存产品可能出现性能下降、外观褪色等问题,最终不得不降价销售甚至报废处理,造成巨大的材料与资金浪费。
2. 原材料过期失效
树脂、固化剂等原材料通常具有一定的保质期,若企业采购计划不合理,导致部分原材料长期闲置于仓库,超过保质期后其性能会发生劣化,无法再用于生产合格产品。尤其是一些特殊配方的树脂,价格昂贵,一旦过期损失惨重,这无疑是材料浪费的又一重要源头。
二、玻璃钢吸收塔生产中材料浪费的原因分析
(一)生产技术与工艺局限
1. 传统工艺精度低
部分玻璃钢吸收塔生产企业仍沿用传统的手工糊制、简单机械加工等工艺,这些工艺对材料用量的控制精度较差,难以实现精细化生产。例如,手工糊制过程中,工人凭借经验进行树脂调配与涂抹,很难保证每一次操作的树脂用量都能精准控制在理想范围内,从而容易造成材料浪费。
2. 模具设计与制造不合理
模具是玻璃钢成型的关键工具,若模具设计存在缺陷,如尺寸偏差、脱模困难等,会导致生产过程中材料填充不均匀、多余材料难以清理等问题,进而增加材料损耗。同时,一些低质量的模具在使用过程中易磨损变形,影响产品尺寸精度与表面质量,迫使企业在修整产品时切除过多边缘材料,造成浪费。
(二)企业管理与员工意识问题
1. 成本核算与考核体系不完善
一些企业的成本核算过于粗放,未能将材料成本细化到每一个生产环节与产品个体,使得基层员工对材料浪费的危害认识不足,缺乏节约成本的积极性。同时,缺乏有效的绩效考核机制来约束员工的操作行为,即使出现材料浪费现象,也未对相关责任人进行及时处罚,导致浪费行为屡禁不止。
2. 员工技能培训不足
玻璃钢生产涉及多种复杂工艺与材料特性,部分企业忽视对员工的专业技能培训,新入职员工不能熟练掌握生产工艺要点与材料使用方法,老员工也难以跟上新技术、新材料的发展步伐。操作不熟练、工艺执行不到位必然引发材料浪费问题,如在树脂传递模塑(RTM)工艺中,若员工对注射参数设置不当,可能导致树脂流淌不畅、充模不满,需要补充注射树脂,造成材料浪费。
(三)供应链协同不畅
1. 原材料供应商管理不善
若企业与原材料供应商之间缺乏紧密的沟通协作,供应商提供的原材料质量不稳定、包装规格不统一,会给企业的生产带来诸多不便。例如,不同批次树脂的粘度、固化时间差异较大,企业需频繁调整生产工艺参数,稍有不慎就会造成材料浪费;而包装破损、标识不清的原材料在储存与使用过程中也容易出现混淆、变质等问题。
2. 上下游信息共享滞后
在玻璃钢产业链中,上下游企业之间的信息传递存在延迟与失真现象。下游客户对吸收塔产品规格、数量需求的变更不能及时反馈给生产企业,导致企业已按原计划采购并储备了大量原材料;或者上游原材料价格波动、供应短缺等信息企业未能提前知晓,只能临时调整生产计划,这两种情况都极易引发材料积压或短缺,最终造成浪费。
三、减少玻璃钢吸收塔生产中材料浪费的应对策略
(一)优化生产技术与工艺
1. 引入先进生产设备与自动化技术
采用高精度的计量设备、自动化的物料输送系统以及智能控制系统,能够显著提高生产过程中的材料控制精度。例如,利用自动化的树脂喷涂设备代替手工糊制,可根据预设参数精确控制树脂用量与喷涂厚度,减少人为因素导致的树脂过量使用;在玻璃纤维缠绕工艺中,引入数控缠绕机,通过精确设定缠绕角度、张力与层数,确保纤维均匀分布,避免过度铺设造成的浪费。
2. 改进模具设计与制造工艺
加强模具设计的科学性与合理性,运用计算机辅助设计(CAD)、模拟分析等手段优化模具结构,确保产品在成型过程中材料能够均匀填充、顺利脱模。同时,选用优质模具材料与先进制造工艺,提高模具的耐磨性与使用寿命,减少因模具问题导致的材料损耗。例如,采用高性能的复合材料制作模具,可有效降低模具变形风险;对模具表面进行精细加工与镀铬处理,能提高脱模性能,减少产品表面修整时的余料切除量。
(二)强化企业管理与员工培训
1. 建立精细化成本管理体系
企业应将材料成本核算细化到每一个生产工序、每一批产品甚至每一名员工,通过成本数据分析找出材料浪费的关键节点与环节。制定严格的成本预算与控制制度,将材料节约指标纳入绩效考核体系,对节约成本的员工给予奖励,对浪费材料的行为进行严肃处罚,从制度层面激发员工节约材料的积极性与主动性。
2. 加强员工技能培训与素质教育
定期组织员工参加专业技能培训课程与实操演练,邀请行业专家讲解玻璃钢生产工艺原理、材料特性以及先进的操作技巧,提高员工的业务水平与操作熟练度。同时,开展企业文化教育活动,培养员工的节约意识与责任感,让每一位员工都认识到节约材料不仅是企业降低成本的需求,更是关乎资源可持续利用与社会发展的大事。例如,举办“节约材料月”活动,通过案例分享、竞赛评比等形式,营造全员参与节约的良好氛围。
(三)加强供应链协同管理
1. 优化原材料供应商管理
建立严格的供应商筛选与评估机制,选择质量可靠、信誉良好、供应稳定的原材料供应商,并与之签订长期合作协议。加强对供应商的质量监督与管理,定期对原材料进行抽检检验,要求供应商提供详细的产品质量报告与使用说明,确保原材料符合企业生产要求。同时,推动供应商优化包装设计,采用标准化、便于储存与使用的包装形式,减少原材料在运输与储存过程中的损坏与浪费。
2. 构建上下游信息共享平台
借助信息化技术搭建产业链上下游信息共享平台,实现企业与供应商、客户之间的实时数据交互。客户可及时将产品需求变更信息传递给生产企业,企业据此调整生产计划与原材料采购量;企业也能提前获取原材料市场动态信息,合理安排库存与采购策略。例如,通过实施企业资源计划(ERP)系统与供应链管理系统(SCM)的集成应用,打通信息壁垒,提高供应链整体协同效率,有效降低因信息不畅导致的材料浪费风险。
综上所述,玻璃钢吸收塔生产中的材料浪费问题是一个涉及生产技术、企业管理以及供应链协同等多方面因素的复杂难题。只有通过全面深入地分析浪费原因,针对性地采取优化生产工艺、强化企业管理、加强供应链协同等一系列措施,才能有效减少材料浪费,实现玻璃钢产业的绿色、高效、可持续发展,在保障企业经济效益的同时,为资源节约与环境保护贡献一份力量。
玻璃钢吸收塔生产中的材料浪费:现象、原因及应对策略
在工业生产***域,玻璃钢吸收塔因其卓越的耐腐蚀性、轻质高强以及******的综合性能,广泛应用于化工、环保等行业的废气处理与净化环节。然而,在其生产过程中,材料浪费问题却如同隐藏在暗处的“利润杀手”,不仅增加了生产成本,还对资源环境造成了一定压力。深入剖析这一现象,探寻有效解决之道,成为玻璃钢行业可持续发展的关键课题。
一、玻璃钢吸收塔生产中材料浪费的常见表现
(一)原材料过量使用
1. 树脂用量把控失准
树脂作为玻璃钢的关键基体材料,在调配与铺设过程中,若因缺乏精准计量设备或操作人员经验不足,常出现树脂用量超出设计标准的情况。过量的树脂不仅使材料成本攀升,在固化过程中还可能产生气泡、开裂等缺陷,影响吸收塔的整体质量与性能。例如,在一些手工糊制环节,工人为追求施工便利,随意增加树脂涂抹量,导致局部树脂堆积,固化后形成富树脂层,降低了结构层的玻纤含量,削弱了塔体的强度与刚性。
2. 玻璃纤维增强材料过度铺设
玻璃纤维是赋予玻璃钢高强度的主要骨架材料,但在生产中,部分企业为保证产品所谓的“***强度”,往往过度铺设玻璃纤维布或毡材。一方面,过多的玻纤增加了材料的消耗与成本;另一方面,不合理的铺设层次与方式会导致纤维分布不均,出现应力集中点,降低产品的稳定性与耐久性。如在缠绕成型工艺里,若缠绕角度、张力控制不当且玻纤层数过多,会使吸收塔在受压时局部受力过***,加速老化破损。
(二)边角废料处理不当
1. 切割余料废弃
在玻璃钢吸收塔的板材切割、零部件加工过程中,会产生***量形状不规则的边角余料。由于这些余料尺寸较小、形状各异,难以直接用于后续生产,许多企业将其当作废弃物处理,这不仅造成原材料的直接浪费,还增加了废料处理成本与环境负担。例如,在制作塔体外壳板时,圆形或弧形板材的边缘切割会留下楔形余料,若不及时回收利用,日积月累数量可观。
2. 不合格品丢弃
生产过程中难免会产生一些不符合质量标准的次品或废品,如内部存在气泡、表面不平整、尺寸偏差过***的吸收塔部件。一些企业缺乏完善的质量管控与修复机制,对这些不合格品简单粗暴地予以报废处理,而实际上部分产品经过适当修补、调整后仍可满足使用要求,这种处理方式无疑加剧了材料浪费程度。
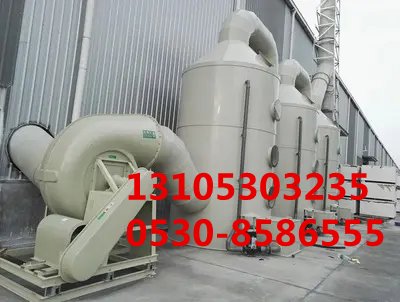
(三)库存积压与过期损耗
1. 市场预测失误导致库存积压
玻璃钢吸收塔的生产周期相对较长,若企业在市场需求预测上出现偏差,盲目扩***生产规模,易造成成品库存积压。长时间存放的库存产品不仅占用***量仓储空间,还需投入人力物力进行维护管理,而且随着时间推移,库存产品可能出现性能下降、外观褪色等问题,***终不得不降价销售甚至报废处理,造成巨***的材料与资金浪费。
2. 原材料过期失效
树脂、固化剂等原材料通常具有一定的保质期,若企业采购计划不合理,导致部分原材料长期闲置于仓库,超过保质期后其性能会发生劣化,无法再用于生产合格产品。尤其是一些***殊配方的树脂,价格昂贵,一旦过期损失惨重,这无疑是材料浪费的又一重要源头。
二、玻璃钢吸收塔生产中材料浪费的原因分析
(一)生产技术与工艺局限
1. 传统工艺精度低
部分玻璃钢吸收塔生产企业仍沿用传统的手工糊制、简单机械加工等工艺,这些工艺对材料用量的控制精度较差,难以实现精细化生产。例如,手工糊制过程中,工人凭借经验进行树脂调配与涂抹,很难保证每一次操作的树脂用量都能精准控制在理想范围内,从而容易造成材料浪费。
2. 模具设计与制造不合理
模具是玻璃钢成型的关键工具,若模具设计存在缺陷,如尺寸偏差、脱模困难等,会导致生产过程中材料填充不均匀、多余材料难以清理等问题,进而增加材料损耗。同时,一些低质量的模具在使用过程中易磨损变形,影响产品尺寸精度与表面质量,迫使企业在修整产品时切除过多边缘材料,造成浪费。
(二)企业管理与员工意识问题
1. 成本核算与考核体系不完善
一些企业的成本核算过于粗放,未能将材料成本细化到每一个生产环节与产品个体,使得基层员工对材料浪费的危害认识不足,缺乏节约成本的积极性。同时,缺乏有效的绩效考核机制来约束员工的操作行为,即使出现材料浪费现象,也未对相关责任人进行及时处罚,导致浪费行为屡禁不止。
2. 员工技能培训不足
玻璃钢生产涉及多种复杂工艺与材料***性,部分企业忽视对员工的专业技能培训,新入职员工不能熟练掌握生产工艺要点与材料使用方法,老员工也难以跟上新技术、新材料的发展步伐。操作不熟练、工艺执行不到位必然引发材料浪费问题,如在树脂传递模塑(RTM)工艺中,若员工对注射参数设置不当,可能导致树脂流淌不畅、充模不满,需要补充注射树脂,造成材料浪费。
(三)供应链协同不畅
1. 原材料供应商管理不善
若企业与原材料供应商之间缺乏紧密的沟通协作,供应商提供的原材料质量不稳定、包装规格不统一,会给企业的生产带来诸多不便。例如,不同批次树脂的粘度、固化时间差异较***,企业需频繁调整生产工艺参数,稍有不慎就会造成材料浪费;而包装破损、标识不清的原材料在储存与使用过程中也容易出现混淆、变质等问题。
2. 上下游信息共享滞后
在玻璃钢产业链中,上下游企业之间的信息传递存在延迟与失真现象。下游客户对吸收塔产品规格、数量需求的变更不能及时反馈给生产企业,导致企业已按原计划采购并储备了***量原材料;或者上游原材料价格波动、供应短缺等信息企业未能提前知晓,只能临时调整生产计划,这两种情况都极易引发材料积压或短缺,***终造成浪费。
三、减少玻璃钢吸收塔生产中材料浪费的应对策略
(一)***化生产技术与工艺
1. 引入先进生产设备与自动化技术
采用高精度的计量设备、自动化的物料输送系统以及智能控制系统,能够显著提高生产过程中的材料控制精度。例如,利用自动化的树脂喷涂设备代替手工糊制,可根据预设参数***控制树脂用量与喷涂厚度,减少人为因素导致的树脂过量使用;在玻璃纤维缠绕工艺中,引入数控缠绕机,通过***设定缠绕角度、张力与层数,确保纤维均匀分布,避免过度铺设造成的浪费。
2. 改进模具设计与制造工艺
加强模具设计的科学性与合理性,运用计算机辅助设计(CAD)、模拟分析等手段***化模具结构,确保产品在成型过程中材料能够均匀填充、顺利脱模。同时,选用***质模具材料与先进制造工艺,提高模具的耐磨性与使用寿命,减少因模具问题导致的材料损耗。例如,采用高性能的复合材料制作模具,可有效降低模具变形风险;对模具表面进行精细加工与镀铬处理,能提高脱模性能,减少产品表面修整时的余料切除量。
(二)强化企业管理与员工培训
1. 建立精细化成本管理体系
企业应将材料成本核算细化到每一个生产工序、每一批产品甚至每一名员工,通过成本数据分析找出材料浪费的关键节点与环节。制定严格的成本预算与控制制度,将材料节约指标纳入绩效考核体系,对节约成本的员工给予奖励,对浪费材料的行为进行严肃处罚,从制度层面激发员工节约材料的积极性与主动性。
2. 加强员工技能培训与素质教育
定期组织员工参加专业技能培训课程与实操演练,邀请行业专家讲解玻璃钢生产工艺原理、材料***性以及先进的操作技巧,提高员工的业务水平与操作熟练度。同时,开展企业文化教育活动,培养员工的节约意识与责任感,让每一位员工都认识到节约材料不仅是企业降低成本的需求,更是关乎资源可持续利用与社会发展的***事。例如,举办“节约材料月”活动,通过案例分享、竞赛评比等形式,营造全员参与节约的******氛围。
(三)加强供应链协同管理
1. ***化原材料供应商管理
建立严格的供应商筛选与评估机制,选择质量可靠、信誉******、供应稳定的原材料供应商,并与之签订长期合作协议。加强对供应商的质量监督与管理,定期对原材料进行抽检检验,要求供应商提供详细的产品质量报告与使用说明,确保原材料符合企业生产要求。同时,推动供应商***化包装设计,采用标准化、便于储存与使用的包装形式,减少原材料在运输与储存过程中的损坏与浪费。
2. 构建上下游信息共享平台
借助信息化技术搭建产业链上下游信息共享平台,实现企业与供应商、客户之间的实时数据交互。客户可及时将产品需求变更信息传递给生产企业,企业据此调整生产计划与原材料采购量;企业也能提前获取原材料市场动态信息,合理安排库存与采购策略。例如,通过实施企业资源计划(ERP)系统与供应链管理系统(SCM)的集成应用,打通信息壁垒,提高供应链整体协同效率,有效降低因信息不畅导致的材料浪费风险。
综上所述,玻璃钢吸收塔生产中的材料浪费问题是一个涉及生产技术、企业管理以及供应链协同等多方面因素的复杂难题。只有通过全面深入地分析浪费原因,针对性地采取***化生产工艺、强化企业管理、加强供应链协同等一系列措施,才能有效减少材料浪费,实现玻璃钢产业的绿色、高效、可持续发展,在保障企业经济效益的同时,为资源节约与环境保护贡献一份力量。